VTube Communications with BendPro-controlled Benders
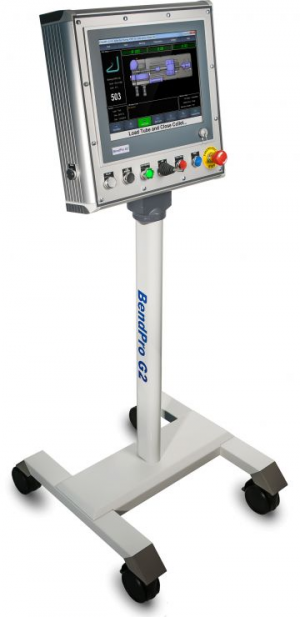 | VTube Communications using Current Tech BendPro G1 and G2 versions.For OEM Benders: - HMT (Horn Machine Tool)
- UTE
- Tubeline
- RbSA
BendPro can use the Supravision Network Protocol as a purchased option. This is the protocol this article assumes. This protocol must be switched on inside the control for the Supravision Network protocol to work as described in this article. |
1 - About BendPro Manual Data File Import
BendPro operators can import Supravision files directly into the part database on the control. The operator enters the FILE window, opens a dialog, and selects the Supravision file to import.
This allows our software to act as a remote programmer for bender data on a BendPro.
VTube-LASER and VTube-STEP can build Supravision files from STEP and IGES models.
G1 Manual File Import: Supravision Type
Follow these steps to import Supravision files:
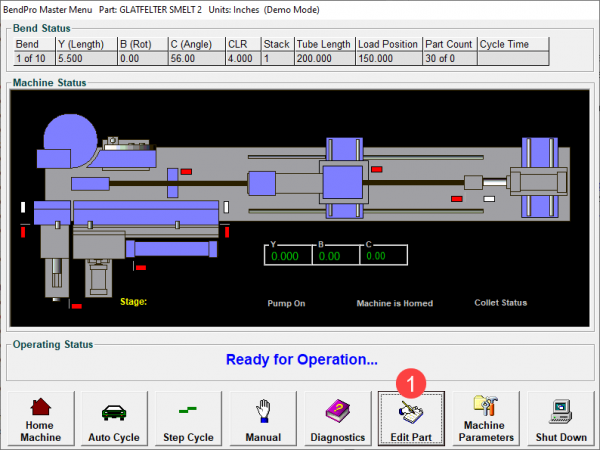
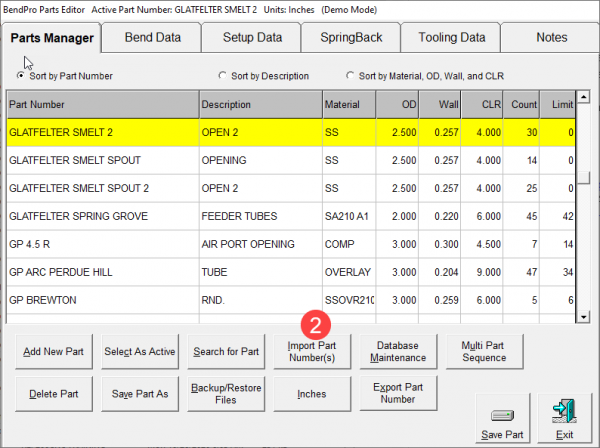
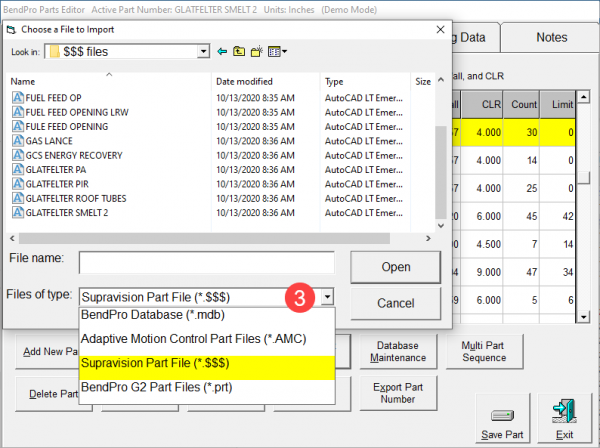
2 - About BendPro Measuring Center Communications
BendPro uses the Supravision Network protocol for communications. Communications are straightforward, efficient, and very fast.
The BendPro can be set up to communicate with HEXAGON or FARO ScanArms running our VTube-LASER software.
How to Check if BendPro G2 Measuring Center Communications Are Possible On Your Bender Control
Utilities - Measure Machine Interface
The Supravision link is sold by Current Tech as an option that can be enabled.
It's important to verify that this option is switched on when discovering if a BendPro G2 is ready for communication. Click on the "Utilities" pulldown menu... |
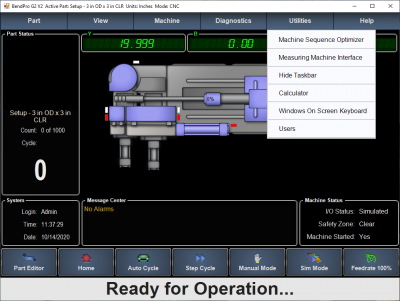
|
...then click on the Measuring Machine Interface option. |
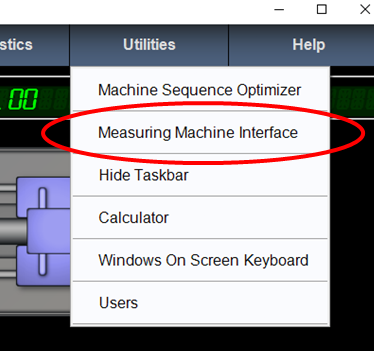
|
If the Enable Supravision Client Interface Option checkbox will allow you to check the box, then your bender has communication capability. | 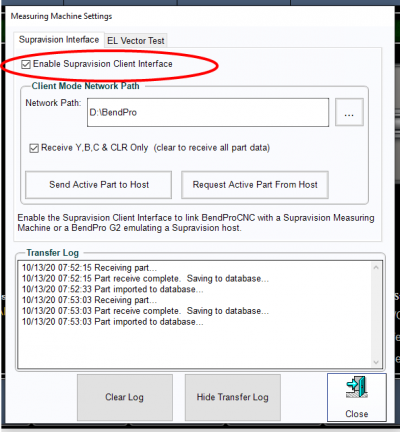
|
If communication is not possible, a software key will need to be purchased from the bender company. Once they send the information, follow these steps: | 1. Download the .key file and save it to the desktop 2. In BendPro G2, go to Help > Menu > Update BendPro 3. Select "I want to update my Activation Key" and click Next 4. Select the .key file from the desktop and click "Open". BendPro G2 will automatically load the update and restart. The communication will now be enabled. |
If the communications are not possible, a software key will need to be purchased from the bender company.
How to Check if BendPro G1 Communications is Possible on Your Bender Control
]G1 Version
Edit Part ButtonVerify that this option is switched on when discovering if a BendPro G1 is ready for communication.
If you are able to open the BendPro to Supravision Link window then your software has communication capability.
Click on Edit Part button in the main screen: |
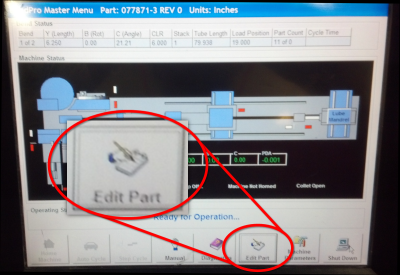
|
Measure Machine ButtonTry pressing the Measure Machine button:
|
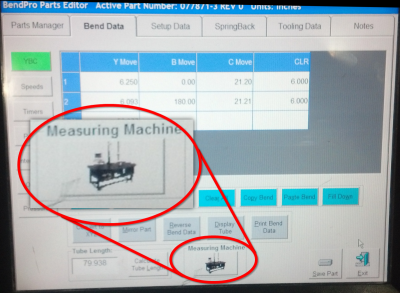
|
BendPro to Supravison Link ScreenIf you can see this BendPro window - then you have communications capabilities on your control.
You can edit the network path for the protocol and also choose and set some communications options. | 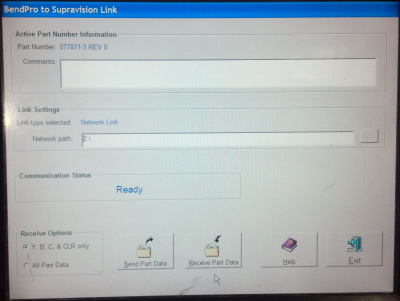
|
How to Setup and Use Communications with BendPro G2
G2 Version Communications Setup
- Enter the Utilities / Measuring Machine Settings menu.
- Put a check in the checkbox to enable communications.
- Set up the path that Supravision Network will use for communications.
- Use the Machine Parameters / General Options to set up the correct bender number. If the bender number does not match the bender number used at the measuring center, communications will not occur.
- The G2 user interface does not need to be in the Measuring Center menu to communicate. However, that menu includes a log that displays the time of the last data transmission. If there are errors, then this is where they will be listed. So it is beneficial to change to that menu before communications.
- In general, it may be a good idea to ENABLE the "Receive Y, B, C & CLR Only" option or the BendPro's setup may be changed in ways that make the bender not run at all.
|
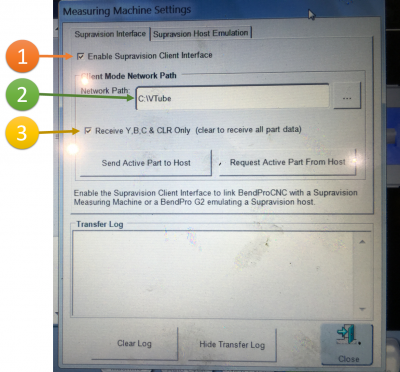
|
This is a closeup of the G2 log after communications:
| 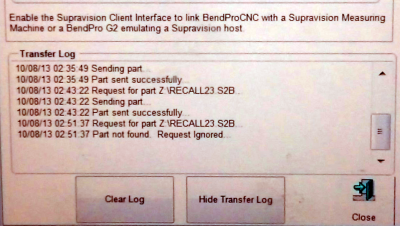
|
G2 Version - DISABLE Host Emulation
Some G2 controls have a Host Emulation tab menu.
It is critical that you are sure that the host emulation mode is disabled - or standard communications will not work properly.
Host emulation mode enables BendPro to act like the measuring center side of the communication. If both Host Emulation' and Client Interface are switched on at the same time, then they interfere with each other.
| 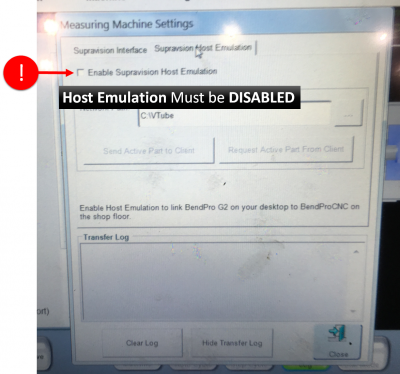
|
G2 Version Communications Rules
The following rules apply for communication using the Supravision Network protocol: - To RECALL data from BendPro, the measuring center must ask for the part with the correct part name - or BendPro will not answer.
- To correct an existing part in the bender, the part must be saved in the BendPro database and must be the active part.
- The part number must have no spaces. The G2 controls will parse the part number so that all letters after the first space are deleted. For example:
"01234 REV0" will be trimmed to "01234". If this new part number does not exist, then the G2 control will ask if you want to import a new part.
- To send a NEW part to the bender, the part number must NOT already be in the database.
- Changing the first straight length will also change the START position for the first bend. If you are using VTube-LASER to correct the bender, and don't want the first or the last straight lengths to change, then manually set the first adjustment to zero in the Bender Setup menu before sending a correction.
| 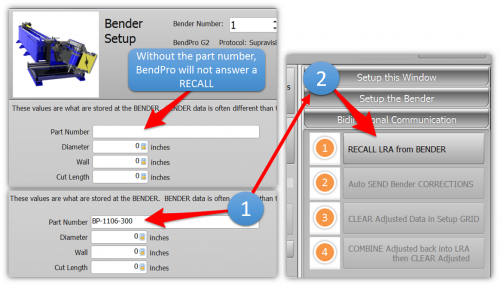
|
How to Setup Benderlink inside VTube for Communications
- Go to System options and find the "Benders" tab.
- Click on "Setup Benderlink Network"
| 
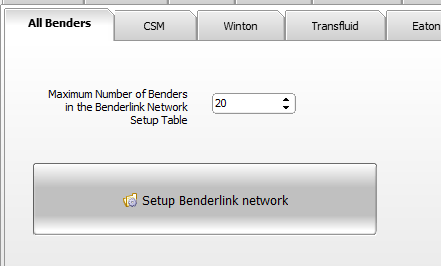 |
- Change the Name to something that will identify the bender
- Change the Protocol to BendPro SVNet
| 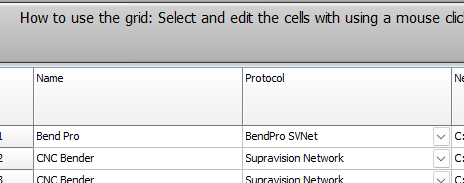 |
- Change the Network Path to a shared network path that can be accessed by both the VTube computer and the bender control. The connection can be wireless or through an ethernet cable. *The path shown is an example path*
- The NetPath Type should stay as "Standard Path"
|  |
- The COM Port should stay at 1 for BendPro controls.
- Timeout Seconds can be increased if there is a slow connection. As a default, VTube looks for data from the bender for 10 seconds before timing out.
- SV No Wait should be set to No for BendPro controls.
- Part Name Match must be set to Yes.
- Ping IP Address allows users to ping the control from the VTube computer. This is not necessary but can speed up the recall process.
| 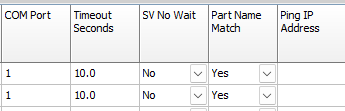 |
- Number at Bender must be whatever number is associated with the bender. For BendPro, this can be found in the system options.
- CW Rotations Positive at Import should only be YES if the positive rotation on the bender is CCW
- CW Rotations Positive at Export should only be YES if the positive rotation on the bender is CCW
- Ignore Incoming Linear Unit should be set to No
- Login Username is a note section for users to track the benders login username
- Login Password is a note section for users to track the benders login password
| 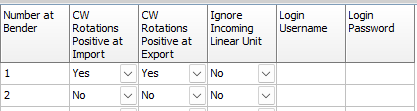 |
How to Setup and Use Communications on the BendPro G1
G1 Version Communications Setup
- Starting from the main screen, press the Edit Part button at the bottom of the screen.
- Press the Measuring Machine button to enter the Supravision Network screen (see the image on the right).
- Set up the path that Supravision Network will use for communications.
- Use the Machine Parameters / General Options to set up the correct bender number. If the bender number does not match the bender number used at the measuring center, communications will not occur.
| 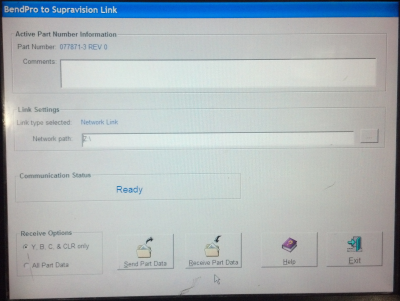
|
G1 Version Communications Rules
The following rules apply for communication using the Supravision Network protocol: - Unlike the G2 user interface, the G1 Supravision window must be displayed during communications. The menu includes a single line that displays if communication works.
- Spaces are allowed in the part number - but NOT recommended. If the number of spaces doesn't match, the communication will fail. It is difficult to differentiate between one space and two spaces, and the G1 can have spaces AFTER the part name - which is not discernable until you enter the keyboard to edit the name. Recommendation: Replace the spaces with underscores.
- AFTER a send from the measuring center to the bender, the operator must walk out to the bender and press the RECEIVE PART DATA button.
For VTube-LASER SEND, there is no timeout. For Supravision or DOCS, if the timeout occurs before the operator arrives at the bender to press the button, then DOCS and Supravision will delete the data file - and the communications will fail.
If there are errors, then this is where they will be listed.
- To correct an existing part in the bender, the part must be saved in the BendPro database and must be the active part.
- The part number must NOT be in the database to send a NEW part to the bender.
- Changing the first straight length will also change the START position for the first bend. If you are using VTube-LASER to correct the bender, and don't want the first or the last straight lengths to change, manually set the first adjustment to zero in the Bender Setup menu before sending a correction.
|


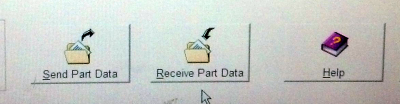
|
General Communications Notes
Part Note Length Limitation
BendPro operators can easily type in a very long part note: - The older Supravsion software (on a ROMER or MM5000 measuring center) will shut down without warning if it receives a part note with more than 95 characters.
- VTube-LASER can handle any part note length.
|
|
Speed and Centerline Radius Fields Observed
- BendPro returns the YBC axis SPEEDS in the Supravision data transfer. This data should be observed and returned from any Benderlink system - or the speeds may be reset to a new value during the following correction. For this reason, it is a good idea to always perform a RECALL before SENDING data corrections to a BendPro control.
- BendPro will use the incoming Centerline Radius values in the Supravision transmission (rather than the values on the tool page). This data should be observed and returned from any Benderlink system - or the radii may be reset to the new incoming vale during the following correction. For this reason, it is a good idea to always perform a RECALL before SENDING data corrections to a BendPro control.
|
|
Non-Bending YBC Row Avoidance Moves
BendPro operators sometimes use non-bending YBC data rows to enable special avoidance moves.
- Supravision and DOCs cannot handle data with avoidance moves inserted in the YBC data. It is necessary to make manual corrections in these cases.
- VTube-LASER uses a data mapping feature to allow for any number of non-bending rows.
|
|
Handling Inverted Rotations
- DOCs software will sometimes invert rotations (to move in the opposite direction) - especially when making rotation corrections around the 180-degree area. Be aware of this, and be prepared to reset any rotation moving in the wrong direction.
- Supravision observes and maintains the rotation direction found at the bender.
- VTube-LASER allows operators to check an Invert checkbox to invert any rotation corrected to the opposite direction. Operators of VTube should observe any rotation that is close to 180 degrees to check for the possibility of the need for inversion. This gives operators complete control over the rotation direction during the correction.
|
|
How to Recall Data from BendPro to Become Master Data
It is possible to recall data from the BendPro to make it the MASTER data at VTube-LASER using these steps. Be sure that the BendPro is ready for communications before you perform a recall.
1 - Enable Communications At BendPro
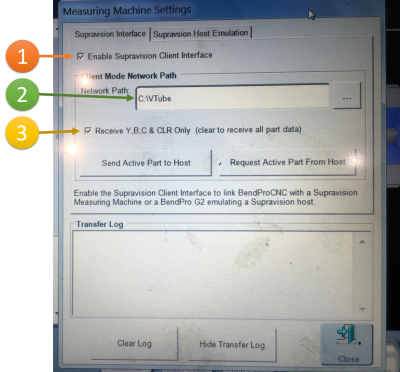
2 - Use the VTube-LASER Bender Setup Screen to Recall Master XYZ
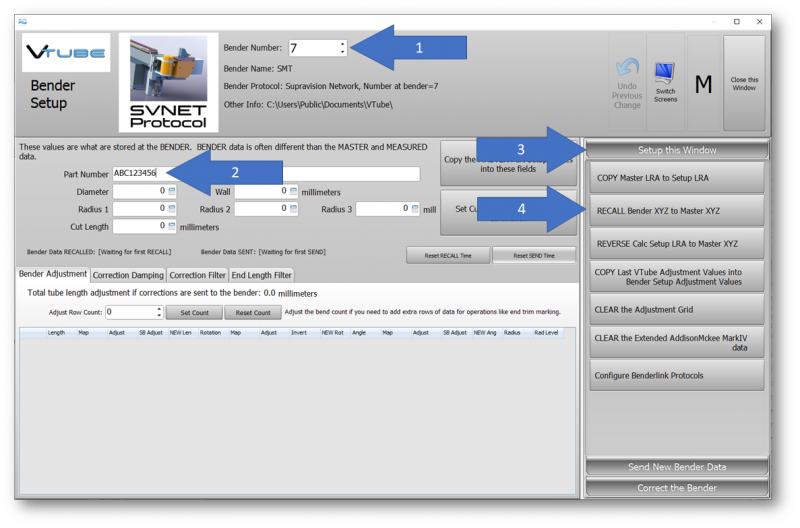
- Select the bender number in Bend Setup.
- Enter the part number to recall. This name must match a name in the BendPro database.
- Click on Setup this Window.
- Click on RECALL Bender XYZ to Master XYZ.
3 - VTube-LASER will Wait for the Data
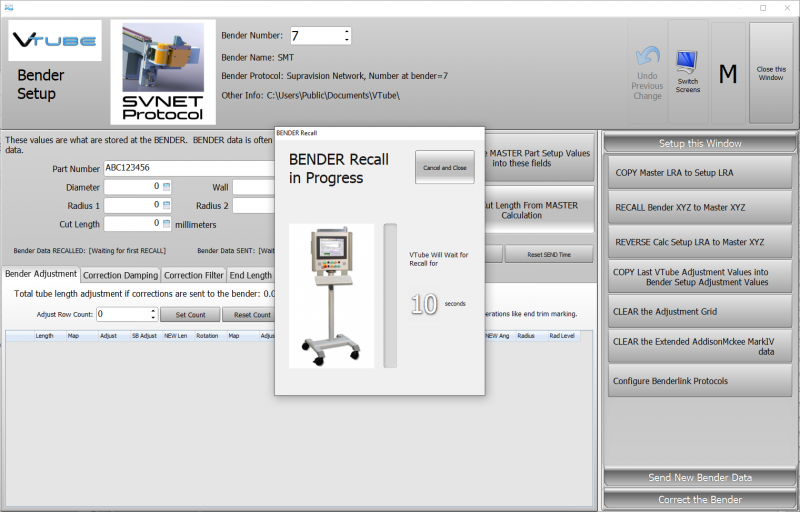
4 - BendPro will Answer with Data
If the part exists at the BendPro, then it will answer with the part, and VTube-LASER will display this message:
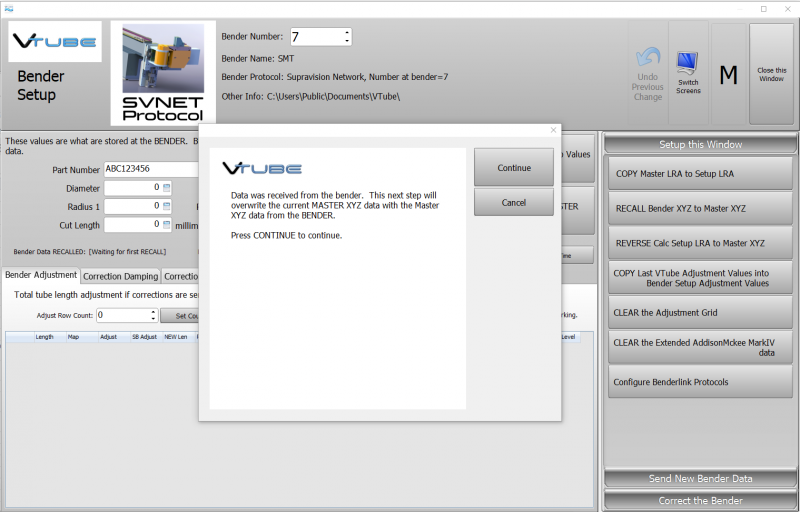
5 - VTube-LASER Will Close the Bender Setup Screen and Display the MASTER Data
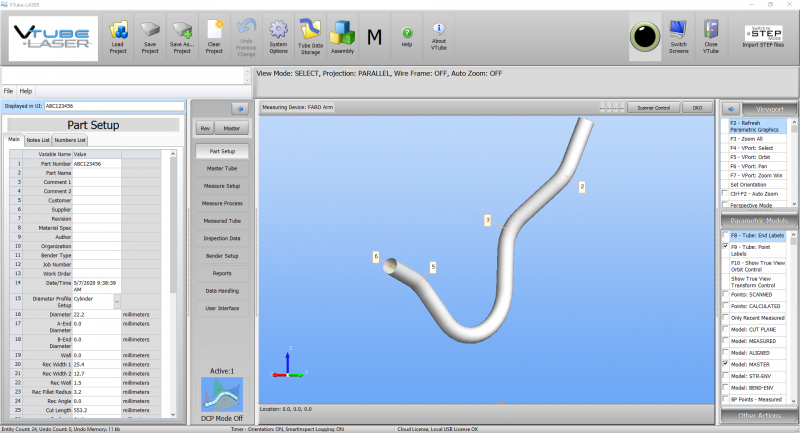
If you do not see an image, then be sure that Model: MASTER has a checkmark and then press F2-F3. Also, you can check in the Master Tube menu for new coordinates.
6 - Save the new VTube-LASER Project File
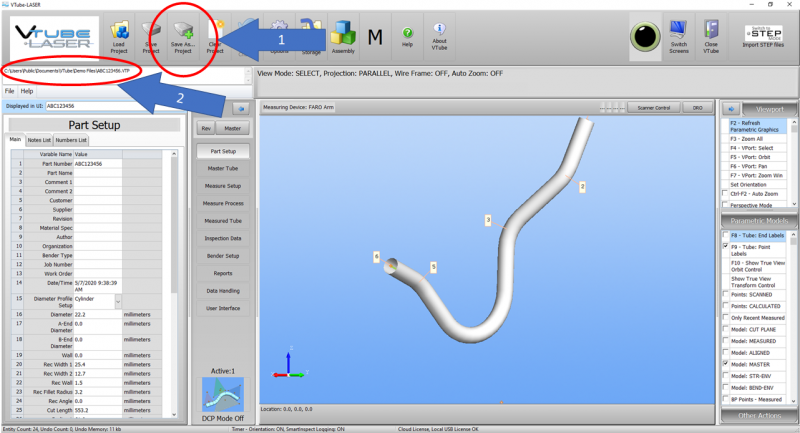
How to Assign Default Options in BendPro G2
These steps allow you to set up BendPro Default Options for reuse when setting up new parts.
See also BPG2_Supravision_Import_With_Material_Specification.pdf Current Tech notes on how to use Material Specification to automatically choose the correct tools in Bend Pro
This feature of the BendPro Part Editor is essentially everything about a part other than part geometries - information such as the Tools information (CD and PD lengths, collet depth, etc.), Load and Unload information, Enables, Springback, etc. The Setup Tables and the Default Table are easy to access and use.
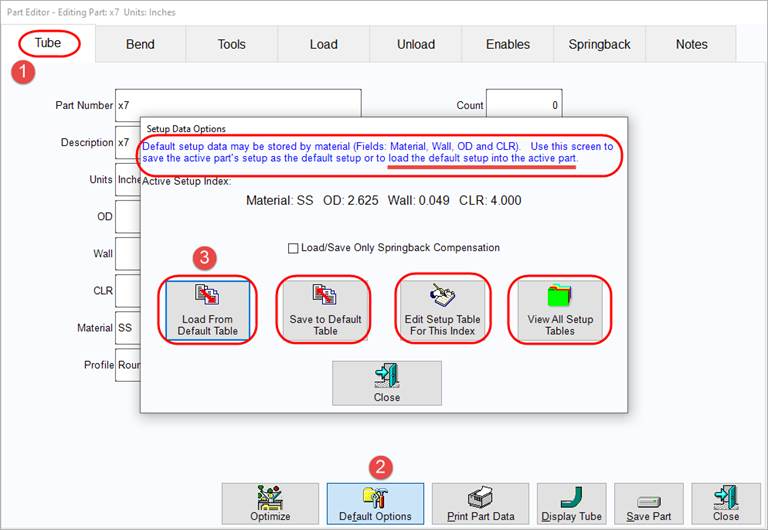
These three selections are associated with the default table:
- The default table information is applied to the Active Part if the "Load From Default" table is selected.
- If Save to Default Table is selected, the current settings of the Active Part are saved to the default table.
- Edit Setup Table edits the current default table.
